Dr. Jenifer Locke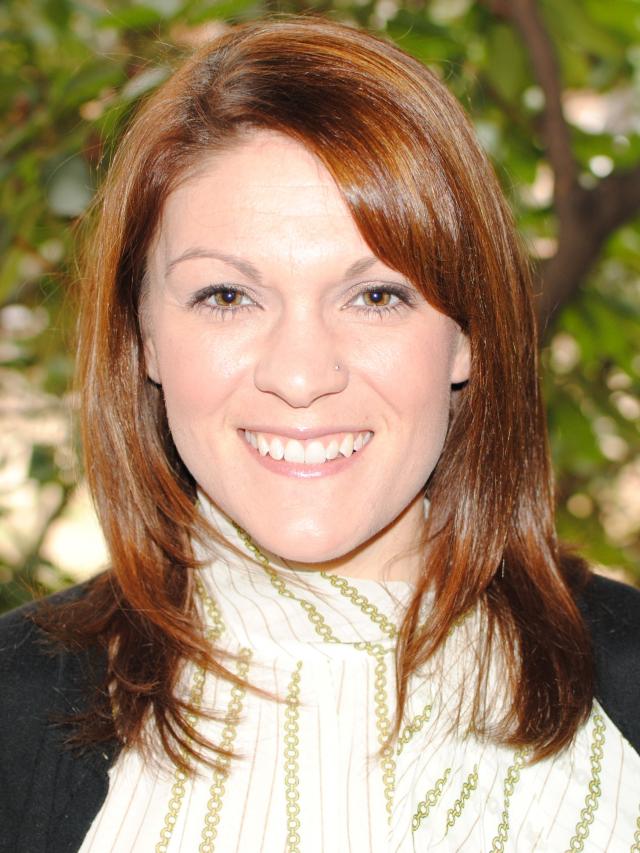
Associate Professor
Department of Materials Science and Engineering
The Ohio State University
About Dr. Jenifer Locke
Dr. Jenifer Locke (she/her) is an associate professor in the Department of Materials Science and Engineering and the Fontana Corrosion Center at The Ohio State University. Prof Locke’s primary research interests are in environment assisted cracking (EAC) and corrosion of metals and alloys. Particularly, she has interest in advancing laboratory EAC experimental capabilities to enable improved understanding of unique service environments, quantifying and
understanding metallurgical and thermo-mechanical processing effects on occluded site electrochemistry in corrosion and EAC of metals, and in inhibition of EAC. Prof Locke’s lab has been funded through programs with ONR, NSF, DoD, and the DoE, as well as industry collaborations with DNV-GL, Arconic, Ford, Honda, INL, PNNL, Battelle, and PPG. Before joining OSU in January 2015, Prof Locke held a position at the Alcoa Technical Center, the R&D facility for Alcoa Inc (now known as Arconic and Howmet). At Alcoa, she worked in alloy development, EAC, and corrosion of aerospace and automotive aluminum alloys. Prior to Alcoa, she received her Ph.D. in Materials Science and Engineering from the University of Virginia in 2010, her B.A. in Physics from Wittenberg University in 2004, and worked for year at the Air Force Research Laboratory at Wright Patterson Air Force Base. Jenifer has won the NSF CAREER and ONR Young Investigator awards and well as the TMS Frank Crossley Diversity Award, AMPP Educator Award in honor of Herbert Uhlig, The Ohio State University’s Lumley Research Award and Mars G. Fontana Teaching Award. Prof Locke has two children aged 8 and 4, and her spouse is an assistant professor in biomedical engineering at OSU. Along with her service in her technical research area, she spends time helping to increase representation and ensure equitable treatment of historically excluded individuals.
Abstract
Environment assisted cracking (EAC), both stress corrosion cracking and corrosion fatigue, is a form of material degradation that occurs when a corrosive environment is concurrently present with external and/or internal stresses/strains acting to cause unexpected and unpredicted failure. The main problems that arise when mechanical stresses are present with a corrosive environment are: 1) pits or intergranular corrosion that develop during localized corrosion and can act as stress concentrators to initiate cracking at stresses much lower than the yield or ultimate tensile strength and 2) accelerated cracking at stress levels lower than and rates faster than expected for inert environments. Understanding and preventing EAC are critical to not only preventing unpredicted failure, but also to ensuring the long-term sustainable use of metals in many structural applications. The complex interaction of the environment with a growing crack has been studied for many alloys in many different environments, but a deep understanding relies on the knowledge of occluded conditions within a crack that are difficult or sometimes impossible to quantify. In order to understand why Al-Cu-Mg (2xxx) alloys are more
susceptible to corrosion yet more resistant to EAC than Al-Zn-Mg (7xxx) alloys, a technique to probe the crack tip pH in a growing corrosion fatigue crack was developed that utilizes esphogeal pH probes used by physicians to measure the stomach pH. This talk with discuss this technique, how it was developed, and how it is being utilized to understand EAC in Al alloys. Specifically, results have been gathered showing that at higher fatigue loading frequencies (f), 10 Hz, both alloys have similar high susceptibilities to corrosion fatigue and the measured crack tip pH is similar between 2024-T8 and 7075-T6. Conversely, as f decreases, 7075-T6 continues to have high susceptibility and slightly acidic pH levels develop (as low as 3.5) while 2024-T8 has a low susceptibility and basic pH develops (as high as 11 to 12). These results are in line with working hypothesis that 2xxx alloys possess an intrinsic resistance to corrosion fatigue at lower f as a result of crack wake corrosion that leads to surface Cu enrichment catalyzing cathodic reactions within the crack environment allowing for self-mitigation of the adverse near neutral/acidic crack tip environment present in 7xxx alloys and reducing corrosion fatigue susceptibility by stabilization of a crack tip passive film that can inhibit crack tip corrosion and the production and uptake of embrittling H.