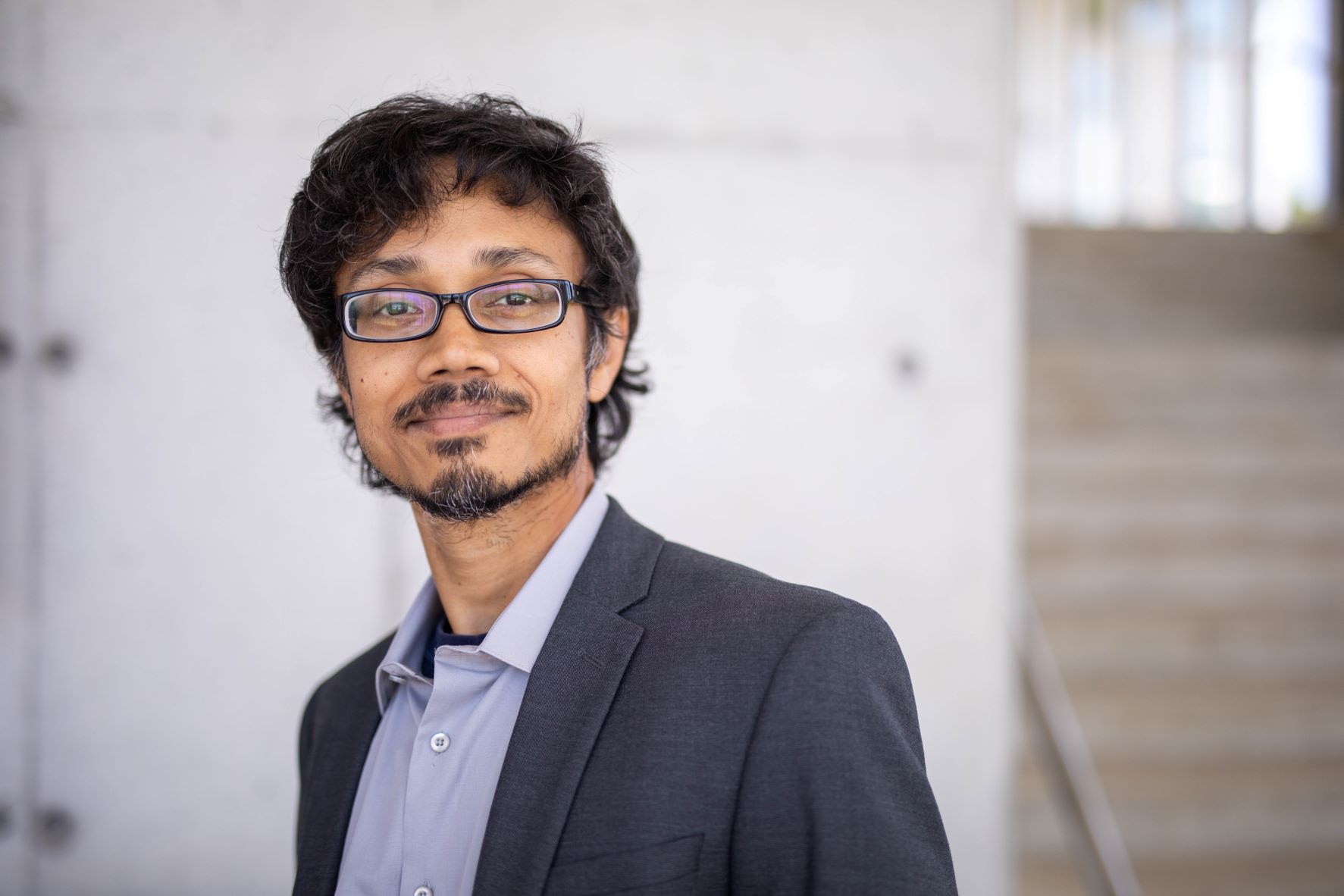
Robotic arms are typically composed of joints, which help the arm move and perform a task. Each of those joints is capable of either rotating or extending—and the number of such possible independent movements is referred to as the robotic system’s degree of freedom. The more joints in the arm, the higher the degree of freedom.
“In general, robotic systems are very high-degree-of-freedom systems,” says Subhrajit Bhattacharya, an assistant professor of mechanical engineering and mechanics in Lehigh University’s P.C. Rossin College of Engineering and Applied Science. “A robotic arm might have 10 different joints. So if you’re trying to make the arm move and grab something, this high degree of freedom—these 10 different joints—present 10 different variables for making that motion. The more variables you have, the more computationally expensive it is to operate that system.”
Bhattacharya is a member of Lehigh’s Autonomous and Intelligent Robotics (AIR) Lab and researches ways to reduce this complexity. He recently won support from the National Science Foundation’s Faculty Early Career Development (CAREER) program for his proposal to use topological abstraction for robot path planning.
The prestigious NSF CAREER award is given annually to junior faculty members across the U.S. who exemplify the role of teacher-scholars through outstanding research, excellent education, and the integration of education and research. Each award provides stable support at the level of approximately $500,000 for a five-year period.
Topology is the mathematical study of properties preserved through the twisting, stretching, and deformation—but not the tearing—of an object.
“The common example is that a donut is equivalent to a coffee mug,” says Bhattacharya. “If the donut was made of Play-Doh, you could squish it and turn it into a mug without making any cuts to it. So what topology does is it abstracts away the geometric information about the precise size without changing the overall shape of the space.”
Bhattacharya uses topology to abstract the complexities (basically, removing the details) presented by all these variables within a robotic system to make operating the systems simpler. So if, for example, you’re using a robotic manipulator with 10 joints and you want it to grab something, topology would reduce the number of variables involved in that motion, and provide the robot with an algorithm that allows it to efficiently and accurately achieve its final destination.
“The output of the algorithm is the sequence of motions,” he says.
Bhattacharya says abstraction is currently being done by others in the field, but in an ad hoc manner. “They’re often very randomized searches. What I’m proposing is a more formal approach of doing abstraction that guarantees optimality and algorithmic completeness, which is a guarantee that we’ll find a solution if a solution exists.”
Robotic systems have become increasingly important in industries such as transportation, manufacturing, and healthcare, and this formalized approach can make those systems even more reliable, says Bhattacharya. In addition, his approach can be broadly applied and used in systems such as those that employ multiple robots or one or more flexible cables, robotics manipulators, and soft robotic arms.
“The ultimate goal is the design of systematic algorithms that can achieve these topological abstractions in an efficient manner, and in a way that is not specific to a particular system,” he says.
It’s an interesting approach, in part, he says, because topology is rarely used in engineering fields like robotics.
“Mathematicians have worked in the field of topology for a long time,” says Bhattacharya, “but in robotics, you rarely see any application of topological methods. So what motivates me is taking this deep mathematical tool and applying it to engineering systems. It’s a relatively rare thing to do, and that’s why I find this research so exciting.”