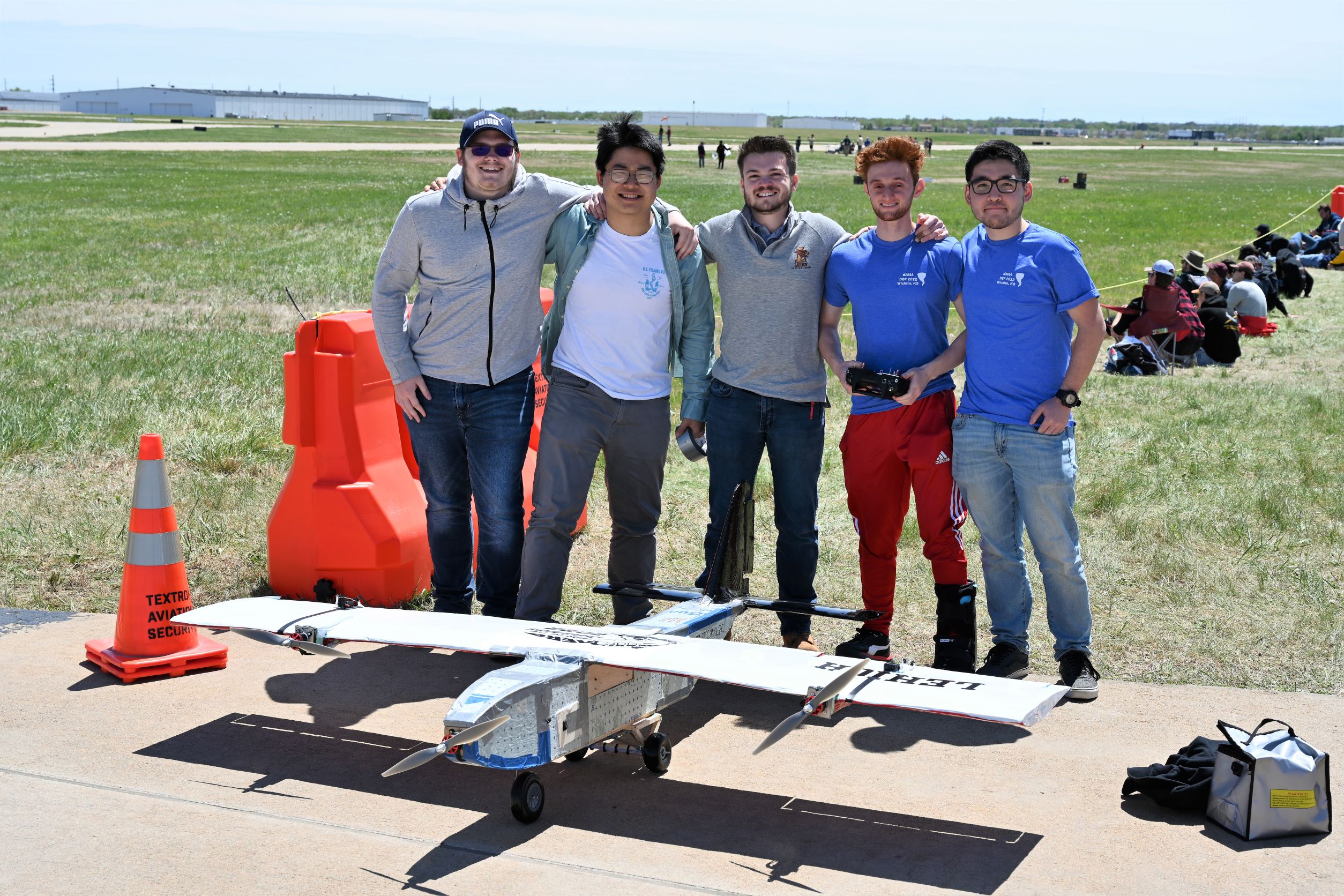
LU Aero, Lehigh’s aerospace engineering club, participated in the 2022 American Institute of Aeronautics and Astronautics (AIAA) Design/Build/Fly Flyoff, held April 21-24. The team placed 48th out of the 65 teams that attended the event, hosted by Textron Aviation, in Wichita, Kansas.
“This was a major milestone for the team, as this was the first time in Lehigh’s history that we attended the competition,” says Alex Perlman ’23, president of LU Aero. “Our team is largely composed of highly-talented underclassmen. This is only the beginning for LU Aero.”
According to the competition website, each year “the objective is to design, fabricate, and demonstrate the flight capabilities of an unmanned, electric powered, radio controlled aircraft that can best meet the specified mission profile. The goal is a balanced design possessing good demonstrated flight handling qualities and practical and affordable manufacturing requirements while providing a high vehicle performance.”
LU Aero was one of 97 teams invited to the Flyoff after finishing 44th out of 127 entries in the proposal phase of the international competition, which focused on developing an aircraft with the capability to remotely deploy force-sensitive packages (specifically vaccination components).

Perlman shared the following account of the team’s experience preparing for and participating in the competition.
Despite a rough start in the Fall semester due to the pandemic, the team worked tirelessly to prepare a final design report in February, while building a first prototype in parallel. This first prototype, dubbed “PhatBass,” utilized water-jetted insulation foam for the fuselage and hot-wire cut styrofoam for the wings. By early March, we regularly performed glide tests and eventually flight tests, destroying and repairing the testbed aircraft many times.
Having exhausted our prototype’s usability and assessing the major points of failure, we made quick design updates and began manufacturing what would become our competition aircraft. This build centered on a sturdy balsa and basswood airframe, but maintained the styrofoam wings.
Simultaneously, other members of the team were manufacturing and testing our package deployment system, consisting of a conveyor belt and a payload door both powered by stepper motors and controlled by an Arduino board.
The team was in a serious time crunch, and as the competition start date of April 21 neared, the possibility of attending seemed increasingly dire. However, in less than a month’s time, the plane was fully assembled, and with just a week before competition, PhatBass performed an outstanding test flight. Thus, the decision was final: LU Aero was going to Wichita.

With a trailer carrying PhatBass and our mobile workshop in tow, we set off for Kansas. The first day of the competition consisted of technical inspections, which required a full pass to even compete in any of the missions. We failed our first inspection but were determined to pass in our next opportunity.
The team had to work late into the night to repair damage taken during the long transit, as well as to integrate last-minute design updates in the conveyor belt and avionics system. We returned early in the morning on day two and passed our second tech inspection with flying colors.
We then joined the queue for the ground mission, which consisted of a timed full loading and deployment of packages. When we rolled PhatBass into the testing zone, we watched in disappointment as our payload door failed to open.
We returned to the hangar and immediately located the point of failure, which had never exposed itself during testing. The team made the fix and returned to the queue but unfortunately, the competition window closed for the day.
That night we compiled a list of potential issues in the deployment system and sought to fix them before our next ground mission attempt to ensure that we’d encounter no more surprises. The team arrived as soon as the doors opened on day three to begin implementing our solutions in the system.
Despite fixing the mechanical issues, our electronics malfunctioned, setting us back again. We worked all day, troubleshooting with our team back at Lehigh, and by midafternoon, the system was performing nominally once again. We joined the ground mission queue but were cut short.
On day four, the final day of the competition, we returned bright and early so as to complete the ground mission as soon as possible. Our number was called and we rolled PhatBass into the testing zone once again. This time, we watched our system perfectly deploy all three packages; we had completed the ground mission.
We immediately joined the long flight line for the opportunity to perform our first flight mission. When it was LU Aero's turn, we carried PhatBass to the runway with confidence. However, a new set of problems in the landing gear quickly exposed themselves, cutting our first flight attempt short.
Determined to showcase our hard work, we got to work replacing the landing gear and by the early afternoon were ready once again. Unfortunately, due to the time constraints and long flight order, we never got that second chance to fly.
Though we did not perform as well as we had hoped, we look forward to being a strong competitor next year, and every year after.
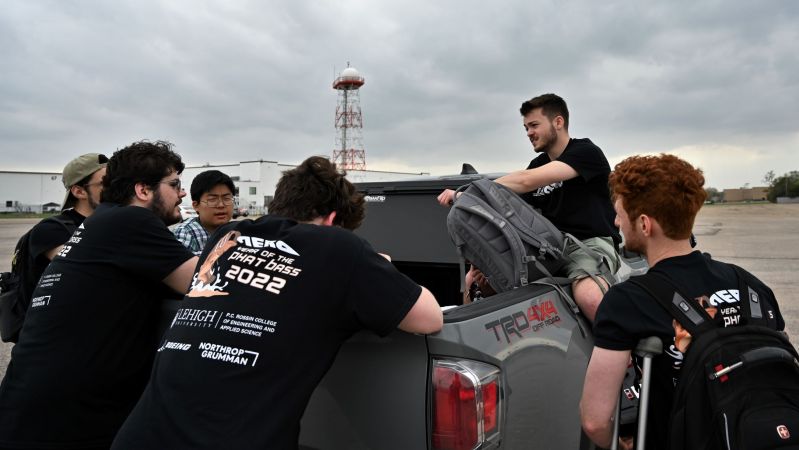