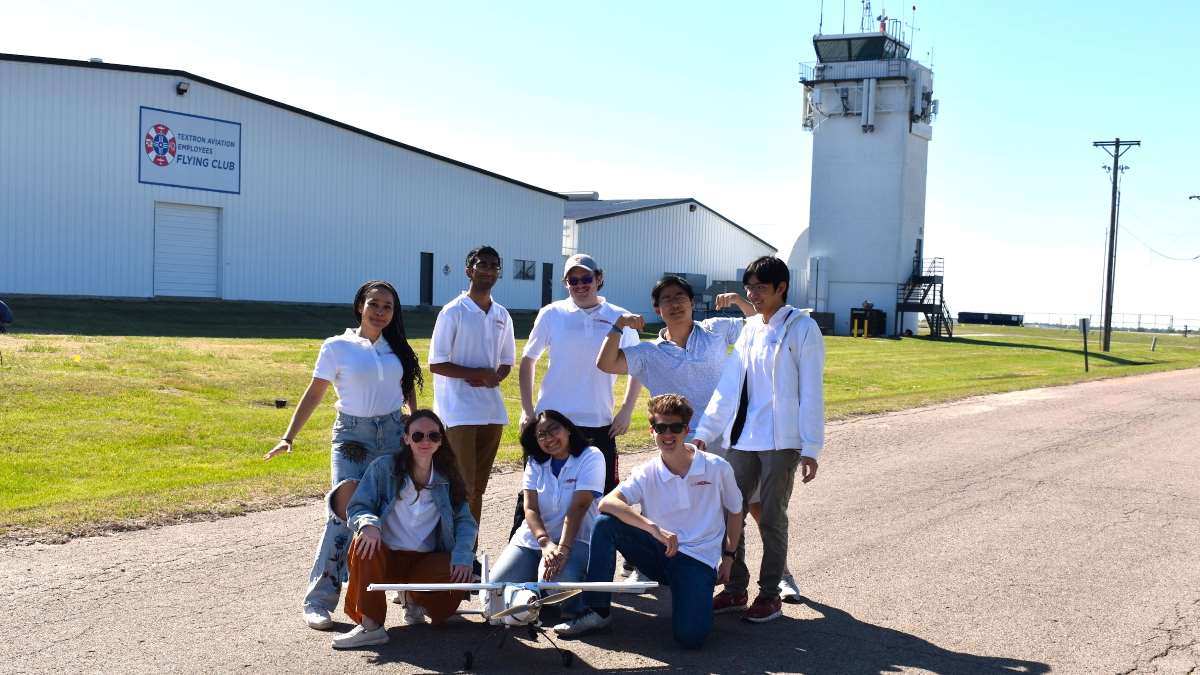
You certainly don’t have to win a competition to sharpen your competitive edge.
That was the case for members of LU Aero, Lehigh’s aerospace engineering club, who participated in this year’s American Institute of Aeronautics and Astronautics (AIAA) Design/Build/Fly Flyoff, held April 18-21 in Wichita, Kansas.
“We experienced quite a few challenges,” says Hayden Kasberger ’25, “but in the end, we learned so much from the other teams at the competition, and now we’ve got a lot of great ideas on how to improve our own aircraft.”
LU Aero was one of 107 teams that participated in the event whose objective is, according to its website, to “design, fabricate, and demonstrate the flight capabilities of an unmanned, electric powered, radio controlled aircraft that can best meet the specified mission profile.”
Teams must undergo a tech inspection of their four-foot remote-controlled aircraft, and complete three flight missions and one timed ground mission.
“The theme for this year was air taxi and medevac,” says Kasberger, who is majoring in mechanical engineering with a minor in aerospace engineering. “And we did pretty well in the ground mission where we had to convert the aircraft into several configurations in a five-minute window.”
For example, the medevac configuration meant arranging a medicine cabinet, two three-inch-tall EMT dolls, and a patient on a gurney into the aircraft, while the air taxi configuration required fitting as many three-inch dolls comfortably into the cabin as possible. The team also had to complete a parking configuration, fitting their aircraft into a limited space.
“The point was to be able to move between these configurations quickly and get the plane ready to fly,” he says.
The eight-member Lehigh team didn’t fare as well in the air, although they were able to complete their first flight mission, and they ultimately finished 63rd. But they took careful notes of their fellow competitors.
“We looked at the design of other teams’ aircraft, and saw how many of them were using a composite construction of carbon fiber, fiberglass, and vacuum-forming plastics,” says Kasberger. “We also learned a lot about how other teams were organized, and how subdividing the tasks between members helped them be more efficient. Those were major takeaways for us. And then on a more basic level, we saw how teams built custom shipping crates for their aircraft that protected them during transport.”
He and the rest of the Lehigh team, which totals about 20 students, plan to spend next year improving their aircraft, experimenting with different designs, construction methods, and prototypes, as well as diving deeper into the basic research that will help guide everything they do.
“Next year, we’ll split up the team into four groups, each assigned their own aircraft. I’ll lead a group that will design an advanced high-speed RC aircraft made of composites, another group will build one made of wood and foam, and we’ll have a group that will create a fully foam plane that we’ll use to teach club members how to pilot.”
For Kasberger, who plans to work in the aerospace industry after graduating next spring, the experience of being part of the club far outweighs the results of a competition. Since joining LU Aero as a first-year student, he’s learned how to use a huge range of tools: from 3D printers to a laser cutter and CNC hot wire cutter, to simulation software like MATLAB and SolidWorks.
“It’s also just so much fun working with other people, discussing design ideas and construction techniques, and then actually building the aircraft,” he says. “I love looking at a structure and thinking about what works and what doesn’t. It really helps you develop that mechanic’s mind.”