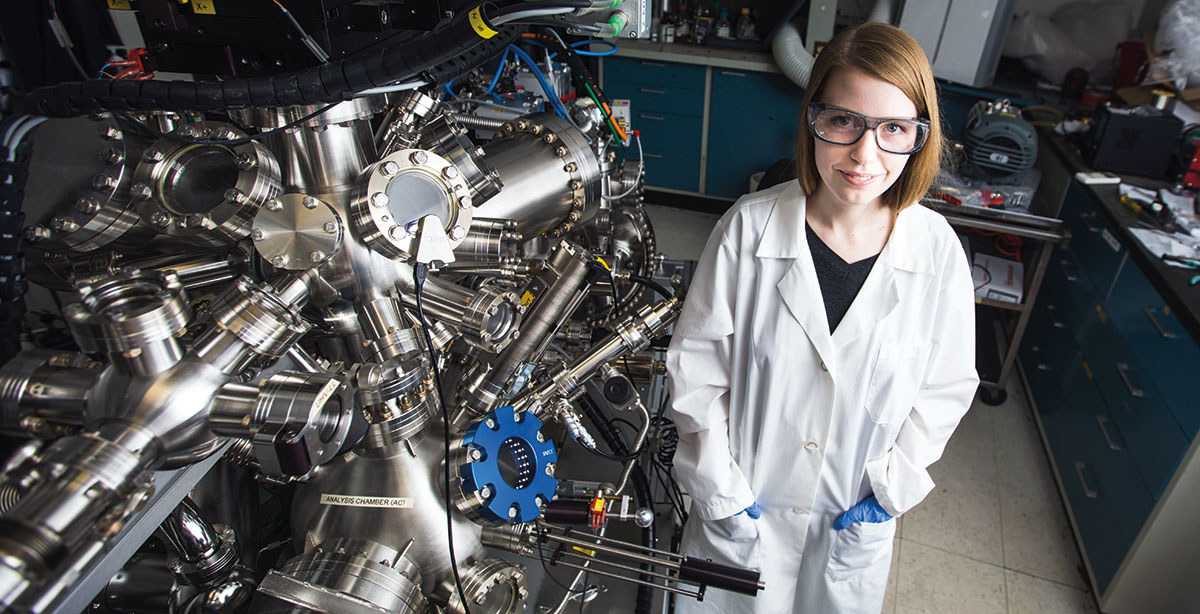
Add olefins to the list of things the world is currently short on.
Olefins are hydrocarbons that serve as the building blocks for products and materials we use every day, like plastics, rubber tires, and liquid fuels.
Chemical plants and petroleum refineries make olefins by using a complex, energy-intensive process called steam cracking. Given the current abundance of natural gas, however, industry has shifted to using lighter hydrocarbon feedstocks from natural gas, which has led to decreased manufacturing of critical chemical feedstocks like butene (4-carbon molecule) and propylene (3-carbon molecule).
One way industry is trying to fill that olefin gap is through ethylene dimerization, a chemical reaction that upgrades shale gas ethylene (2-carbon molecule)—which is both plentiful and cheap in the U.S.—to butene. (Butene can be further converted into propylene, which can be converted into polypropylene for use in plastics; further upgrading of ethylene and propylene can create liquid fuels.) But this is an imperfect process that can utilize liquid acids that cause acid gas emissions, damage equipment, and create separation problems with the final product.
A team of Rossin College researchers recently received a $500,000 grant from the National Science Foundation to study an alternative catalytic process based on solid acid catalysts (ethylene dimerization over a nickel sulfated zirconia catalyst) that does not emit acid gases and avoids separation issues.
“Industry often uses homogeneous systems that can require co-catalysts or liquid acids to carry out the reaction, and those can result in problems like acid gas emissions, separation issues, and entrainment of acids in the end product, which can lead to equipment damage,” says Erin Sobchinsky (photo, top), a PhD student in the Department of Chemical and Biomolecular Engineering and one of the co-authors of the proposal. “One solution is to use heterogeneous solid acid catalysts. They don’t have to be separated from the final product, and they greatly reduce, if not eliminate, the emission of acid gases, which are harmful to the environment."
The catalyst her team is examining— nickel sulfated zirconia, in which nickel and sulfate are impregnated on a zirconia support—is relatively understudied, says Sobchinsky, who is advised by Israel E. Wachs, Lehigh’s G. Whitney Snyder Endowed Professor of Chemical and Biomolecular Engineering. Wachs is the director of Lehigh’s Operando Molecular Spectroscopy and Catalysis Research Laboratory and the principal investigator on the project.
The research approach they are taking is a novel one.
Many of the catalysis studies to date, she says, have been performed under ultrahigh vacuum conditions—meaning at extremely low pressures with almost no gases present around the catalyst—or under ambient conditions, where the catalyst is exposed to a humid atmosphere at room temperature.“
But those conditions really aren’t representative of what the catalysts experience during reaction,” she says. “The surfaces of many catalysts can also restructure, which makes characterization during reaction all the more important.”
Sobchinsky and her team are using in situ and operando molecular spectroscopy (conducting experiments under relevant reaction conditions) to characterize their catalyst. Under these conditions, the researchers can better understand what’s happening on the surface of the catalyst, which is where the reaction takes place.
“Our current work is focused on determining exactly what the surface structures of the catalyst look like during reaction and understanding the synergy between the nickel and sulfate species,” says Sobchinsky. “That will allow us to determine which surface structures are important for enhancing the reaction. We can then rationally design new catalysts with better performance by synthesizing catalysts that contain more of these reaction-enhancing surface structures.”
As Sobchinsky and her team develop a fundamental understanding of what is happening at the molecular level, they’ll be able to fine-tune the molecular structures toward the goal of designing more active catalysts. The more active a catalyst, the more reactant it can convert, with less energy use and impact on the environment or infrastructure.
“This approach to catalysis, although it is at the cutting edge, isn’t always applied by other research groups because of the limited availability of such sophisticated instrumentation,” says Sobchinsky. “Doing these in situ and operando molecular characterization studies is one of the most important ways to move forward in the field.”